EPDM Rubber Extrusion
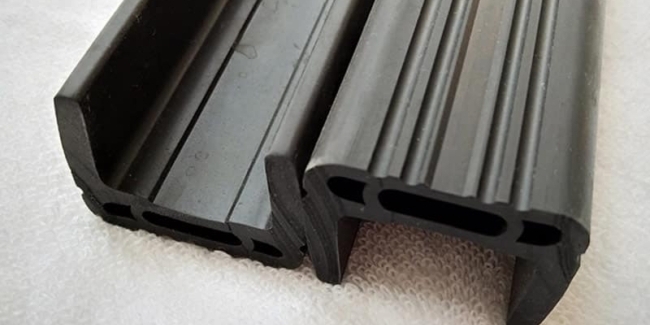
What Are The Key Characteristics of EPDM Rubber Extrusion
- Colour: Black, White/Blue (FDA)
- Available Grades: High Temperature, WRAS Approved, Commercial, FDA
- Density: 40° – 90° Shore Hardness
- Resistances: UV, O Zone, Water
- Temperature Range: 150°C to -500°C (depending on grade)
- Thickness: Any thickness is available on custom made mouldings
Full technical data can be supplied upon request,
or downloaded from our online portal.
Key Features:
- Weather Resistance: EPDM rubber extrusions are highly resistant to environmental factors, including sunlight, rain, and extreme temperatures. This ensures long-lasting performance, even in harsh outdoor conditions.
- Excellent Sealing Properties: EPDM rubber's natural compression set and flexibility allow it to create a reliable and airtight seal. It effectively prevents the ingress of moisture, dust, and contaminants.
- UV and Ozone Resistance: EPDM rubber maintains its integrity when exposed to ultraviolet (UV) rays and ozone, making it suitable for applications that require outdoor durability.
- Temperature Tolerance: EPDM rubber can withstand temperature variations, ranging from extreme cold to high heat, without losing its sealing capabilities or physical properties.
- Chemical Resistance: It offers resistance to a wide range of chemicals, acids, and alkalis, making it suitable for applications where exposure to chemicals is a concern..
EPDM Rubber Extrusion
Advanced Seals & Gaskets Ltd supply a vast and complex range of rubber extrusions, including EPDM rubber extrusions in many grades of material and formats, from simple cords to complex contoured parts, all designed to provide protection, prevent the leakage or ingress of air, fluid or gas and to be aesthetically pleasing as edge trims or buffers.
Customers commonly request that their extrusions are produced in EPDM due to its excellent list of resistance and strength properties. All our EPDM rubber extrusions are made to order and are produced using dimensions, samples or drawings provided by customers to ensure the final product perfectly fits their application.
What are EPDM Rubber Extrusion?
EPDM is a synthetic rubber, an abbreviation of ethylene, propylene, diene and monomer, a durable rubber popular for use in a range of applications, available of grades and hardnesses from 40°- 90° shore (the shore hardness is measured using a shore durometer which indicates the level of resistance to indentation, the higher number on the scale indicate a greater resistance - harder the material/lower number indicate less resistance- softer the material.
‘Extrusion’ is the process of turning raw material in this case EPDM rubber compound into a specific shape using an extruder machine which works using high pressure and a die (a shaped tool). This machine pushes raw material through the die creating the finished extruded rubber profile, in continuous lengths, with a consistent cross-sectional shape as per the customer's design running throughout.
EPDM rubber extrusions can be made as a ‘solid’ shape such as cord, or ‘hollow’ where a hole, usually in the centre runs through the entire length of the EPDM rubber extrusions just leaving the outer wall. Some of the most commonly used extrusions are D-sections, P-sections, door seals, window seals, U-channels and cords, many of which can be supplied with a self-adhesive finish.
Product Enquiry
For information on EPDM Rubber Extrusion please complete the following quick enquiry or call us on +44(0)1384 252555.
Why use EPDM Rubber Extrusion?
There are many different forms and profiles of EPDM rubber extrusions that can be found used within various applications for sealing against air, gas and liquid, cushioning against vibrations & rattles and as surface protection. EPDM rubber extrusions are perfect for applications where off the shelf seals and gaskets will not fit and a bespoke profile or shape is required. EPDM rubber extrusions are also the quickest and simplest way to create lengths of identical products even when manufactured in bulk, which is essential for high volume production and assembly.
By using an EPDM rubber extrusion, end users have the benefit of a perfectly fitting rubber profile combined with the properties of the EPDM material which include an operating temperature range of -30°C to + 110°C, resistance to environmental effects of UV rays, O-zone and weathering making this a great material for both internal and external applications.
The Advantages of Using EPDM Rubber Extrusion
There are many advantages to using EPDM rubber extrusions within your application, namely its extensive list of properties and the variety of grades available. EPDM rubber extrusions are ideal for use where a strong, versatile material is required in an environment where there may be exposure to the ozone, UV, chemicals, water, steam and acids.
EPDM rubber extrusions are readily available in a range of standard profiles, however, more complex and bespoke profiles will take longer to supply due to the process of designing and making the tool, testing samples and then making the final product. seals such as mouldings and extrusions will take longer due to the processes entailed.
The tear resistance of the material allows the extrusion to be produced, cut down and pushed into position without damage or distorting the final product or causing the seal to fail.
Benefits of EPDM Rubber Extrusion
- Ozone and Weather Resistant
- Durable
- Variety of grades and hardnesses available
- Resistance to Fine Particles
- Can be extruded into bespoke designs
- Creates an air and watertight seal
Different Grades
Advanced Seals & Gaskets work with many material manufacturers and suppliers, giving our customers more choice when designing their EPDM rubber extrusion, other grades available include:
FDA grades - Food quality EPDM is available in blue and white options. This synthetic material is suitable for use in food and pharmaceutical processing applications. Food quality EPDM offers good resistance to animal and vegetable oils, iis non-toxic and has a working temperature of -25°C up to +140°C.
WRAS approved EPDM rubber seals are suitable for use in potable water applications (water for human consumption) The material is resistant to weathering, ozone, ageing and chemicals and meets standards BS 6920-1:2000 and BS 6920-1:2014. WRAS approved EPDM has a working temperature of -40°C up to +120°C.
Peroxide Cured - Vulcanising or curing EPDM using peroxide (as opposed to Sulphur) produces a more superior material with higher temperature resistance, heat resistance and improved oil and chemical resistance, this material is suitable for demanding applications such as nuclear facilities.
Please get in touch if you are unsure which grade of EPDM or type of extrusion you require for your application, samples of our materials are readily available for your perusal.
Please contact us using the form below or by calling us on +44(0)1384 252555.