Neoprene Rubber Extrusion
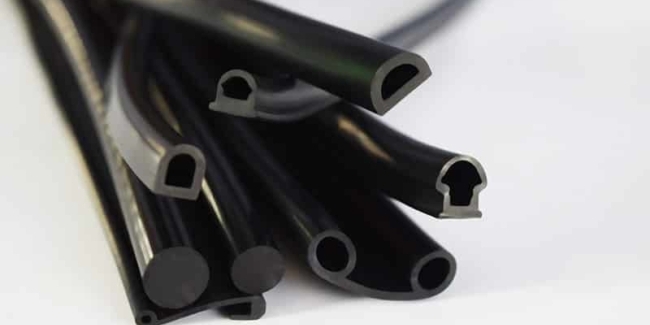
Neoprene Rubber Extrusion
Felt strips offer various advantages due to their exceptional properties, making them valuable in numerous applications.
Felt strips excel in providing protection, sealing against air, fluid, and gas, and preventing leaks. They are aesthetically pleasing and versatile.
Neoprene rubber extrusions are highly sought after by our customers due to their water and environmental resistance, strength, durability, and versatility.
All neoprene rubber extrusions are custom-made, with tooling and samples created to ensure a perfect fit for the intended application.
Neoprene rubber extrusions are ideal for applications exposed to water, chemicals, and oil, including construction, aerospace, automotive, marine, and agriculture.
What is Neoprene Rubber Extrusion?
Utilizing felt strips offers several advantages due to their unique properties, making them indispensable in various applications.
Felt strips are highly effective at noise dampening, cushioning, and padding. These properties make them exceptional for applications requiring sound absorption and noise reduction.
Felt strips are versatile and commonly serve multiple functions simultaneously. When applied for cushioning, they also absorb sound waves, contributing to noise reduction.
For further insights into the myriad advantages of felt strips, don't hesitate to reach out to our dedicated team.
Product Enquiry
For information on Neoprene Rubber Extrusion please complete the following quick enquiry or call us on +44(0)1384 252555.
Product Specification & Key Characteristics
- Colour: Black (white - FDA only)
- Grades Available:standard
- Density: 40 – 90 Shore Hardness
- Resistances: UV, ozone, water, oil, gases
- Temperature Range: -20°C to +70℃
- Thickness: made to order
**Neoprene sponge is not suitable for use with oxidising acids, ketones and some hydrocarbons**
Full technical data can be supplied upon request,
or downloaded from our online portal.
Extrusion
Felt strips offer numerous advantages, making them an ideal choice for various applications. Their exceptional properties, such as noise dampening and cushioning, are highly valuable. Additionally, felt strips are versatile, serving multiple functions concurrently, including sound absorption and noise reduction. If you seek further information on why to use felt strips, please do not hesitate to contact our dedicated team.
Why use Neoprene Rubber Extrusion?
Neoprene rubber seals, including extrusions, provide a consistent material with versatile mechanical properties, making them a favored choice across various industries. Neoprene's exceptional features include creating air, dust, and water-tight seals, resilience to environmental factors, resistance to oil, chemical inertness, flame retardancy, and a wide temperature range. Neoprene rubber comes in various hardnesses and grades, allowing for custom extrusion profiles. This material is highly sought after in automotive applications like door, boot, window seals, and vibration damping.
Benefits of Neoprene Rubber Extrusion
- Popular for external & automotive sealing applications
- Durable
- Variety of Grades & profiles available
- Impermeable to water and dust
- Moderate resistance to oil, chemical greases and fats.
- Excellent resistance to ozone, weathering and ageing
Advantages of Using Neoprene Rubber Extrusion
These Neoprene rubber extrusions are utilised where a durable, strong, abrasive material is required in an environment where exposure or sealing against extreme weather, water, salts, oil grease, UV/Ozone and gases is necessary.
Neoprene rubber extrusions create identical cross-sectional shapes products in varying lengths as required by the customer from short, pre-cut sections, right through to rolls of extruded product 100’s of meters long.
As neoprene rubber profiles are manufactured using raw material, we have the ability to design and offer bespoke and unique profiles to perfectly match our customer's specifications.
Different Grades
Advanced Seals & Gaskets work with many material manufacturers and suppliers, giving our customers more choice when designing their neoprene rubber extrusion. Neoprene rubber extrusions can be supplied in a number of grades and hardnesses, some of the main ones being:
(BS2752) British standard 2752 is a higher performing, stronger grade of neoprene rubber which offers a wider working temperature range of -30°C up to +120°C, greater resistance to ageing, weathering, acids, inorganic salts, oils and ozone as well as improved strength and anti-abrasion qualities in comparison to standard neoprene. This grade is available inshore hardnesses of 40°, 50°, 60°, 70° and 80°.
Flame retardant neoprene rubber extrusions can handle continuous temperatures of -30°C to +100°C, this material meets the test requirements of the flammability standard UL94-V0 and is in line with ISO 340. Flame retardant neoprene rubber sheets are also tested in accordance with anti-static BS 490.
Food Quality (FDA) neoprene is white in colour and conforms to EC and FDA regulations for use within the food processing and pharmaceutical industries. Properties including resistance to fats, greases and vegetable oils, combined with higher tensile strength and wider working temperature range of -30°C up to +130°C make it a popular material to use.
Please get in touch if you are unsure which grade of neoprene or type of extrusion you require for your application, samples of our materials are readily available for your perusal.
Please contact us using the form below or by calling us on +44(0)1384 252555.